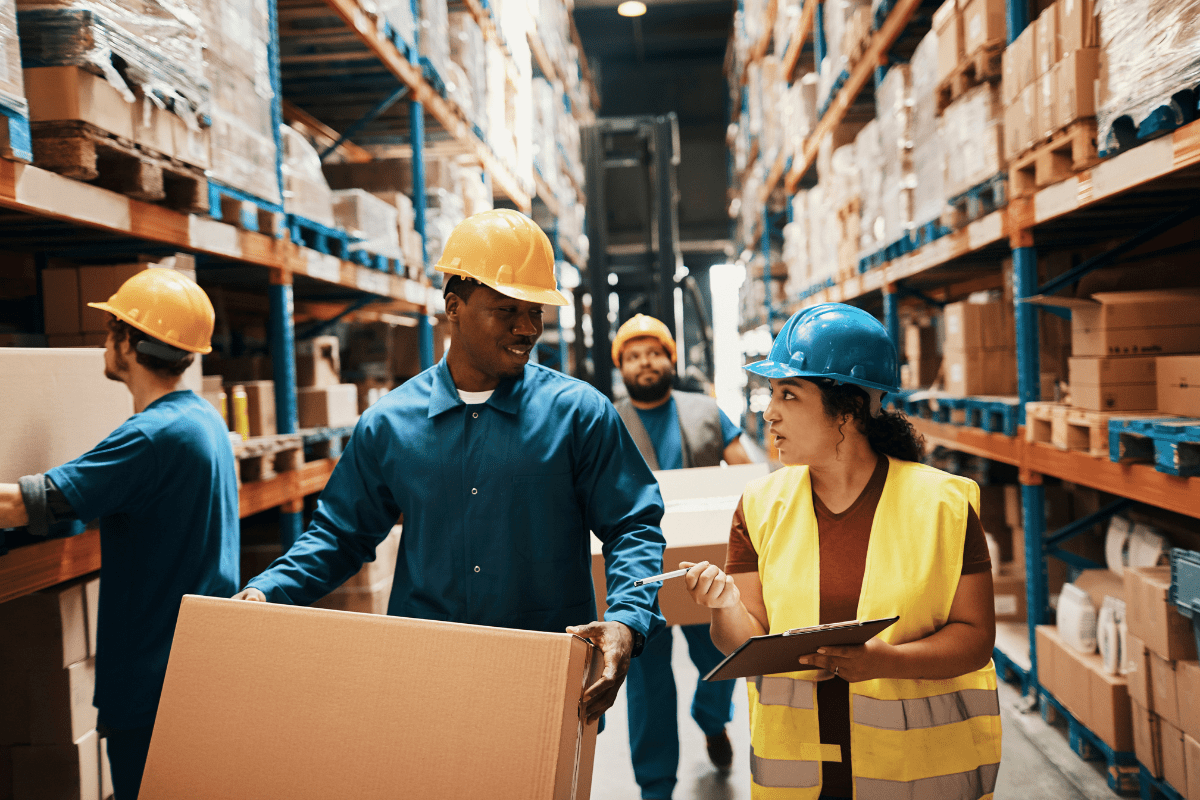
- What’s the difference between leading and lagging indicators in the workplace?
- How can leading and lagging indicators help prevent workplace injuries?
- What are the benefits of using leading indicators to improve your workplace safety program?
- What are some of the most important leading and lagging indicators in workplace safety?
- How can tracking leading indicators improve your safety record?
Most companies are well aware of the pressing costs of workplace injuries—from hospital care to employee absenteeism, the expenses add up, contributing to significant losses in revenue across industries. In 2020 alone, the direct and indirect costs of workplace injuries amounted to a staggering $163.9 billion. With this figure in mind, it’s no wonder that so many industry professionals are looking to increase workplace safety.
Safety organization UL LLC (formerly Underwriters Laboratories) attributes our inability to improve workplace safety to the inaccurate data that is often used to identify and correct high-risk workplace behaviors.
According to their research, “Often, the key obstacle to improvement is a singular focus on lagging indicators of workplace safety…This type of data reflects only the consequence of an unsafe workplace and provides little insight into the root causes responsible for safety incidents. Leading indicators, on the other hand, focus on steps and processes that are designed to prevent an accident or loss from happening in the first place.”
Let’s take a look at how leading indicators can shed light on the effectiveness of health and safety programs and how they can be used by employers to reveal the underlying causes of workplace injury and illness.
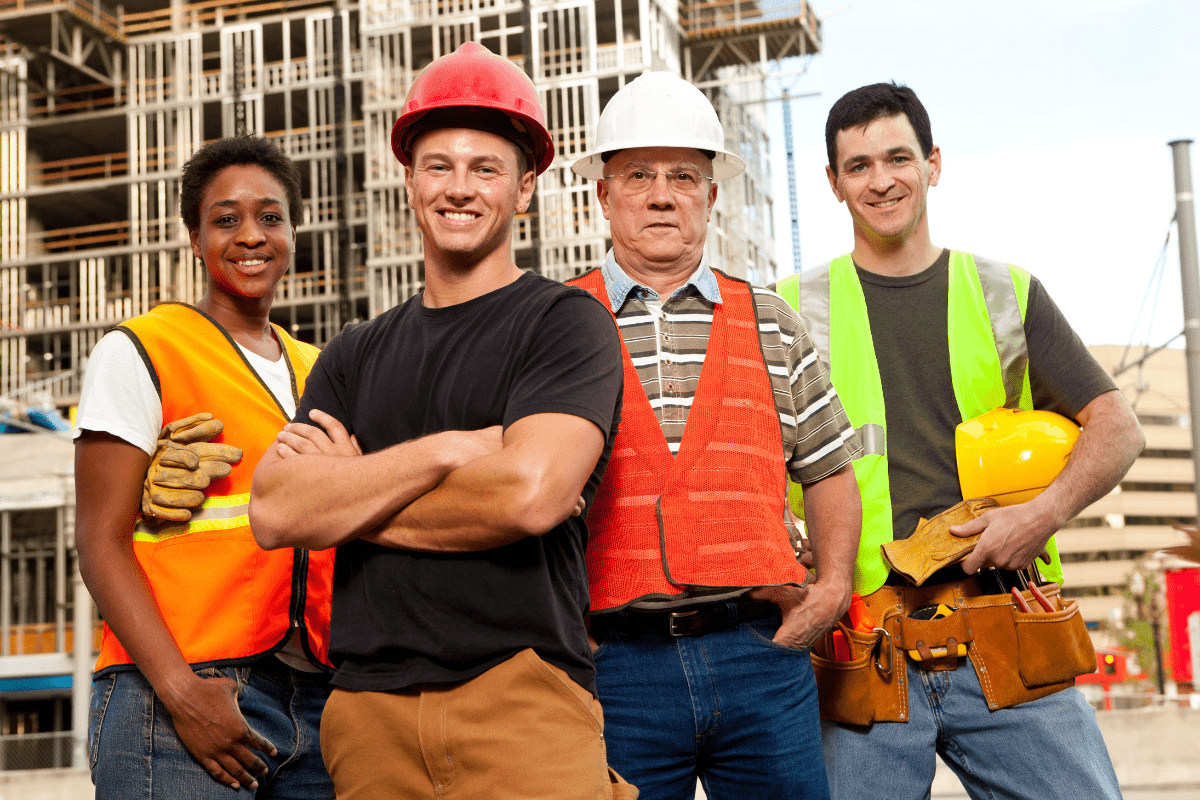
What’s the Difference Between Leading and Lagging Indicators in the Workplace?
Leading indicators are events or measurements that can predict future outcomes and behavioral trends. Lagging indicators are events or measurements that reflect past performance.
By tracing outcomes to their potential source, leading indicators allow companies to take preventative measures to correct behavior that has a high likelihood of resulting in injury. In most cases, leading indicators point to inefficiencies or issues within one of these three areas:
- Employee engagement
- Customer satisfaction
- Process efficiency
On the other hand, lagging indicators show correlations between past events and results, providing a clear picture of their consequences. While helpful for understanding the costs of certain actions, they offer less immediate utility than leading indicators.
Common examples of lagging indicators include:
- Financial Metrics (profit and loss)
- Productivity Metrics (output per hour)
When used in conjunction, leading and lagging indicators can provide a more complete picture of your organization’s performance.

How Can Leading and Lagging Indicators Help Prevent Workplace Injuries?
Leading indicators are invaluable to workplace safety programs because they allow companies to proactively change behaviors, policies, and workflows to prevent injuries before they occur. By tracing the issue to its source, they enable companies to identify and address problematic trends before they become safety incidents. Lagging indicators are also helpful by providing a macro lens for you to analyze how these issues affect your company as a whole.
For example, if you notice that certain tasks or processes are consistently taking longer than expected, leading indicators may show that employees are struggling with outdated processes or inefficient equipment. By addressing these issues, you can reduce the likelihood of accidents caused by frustration, fatigue, or even process workarounds.
When combined with lagging indicators such as injury rates and workers’ compensation claims, the two approaches can identify patterns and trends that may indicate a need for additional training, equipment upgrades, or other interventions.
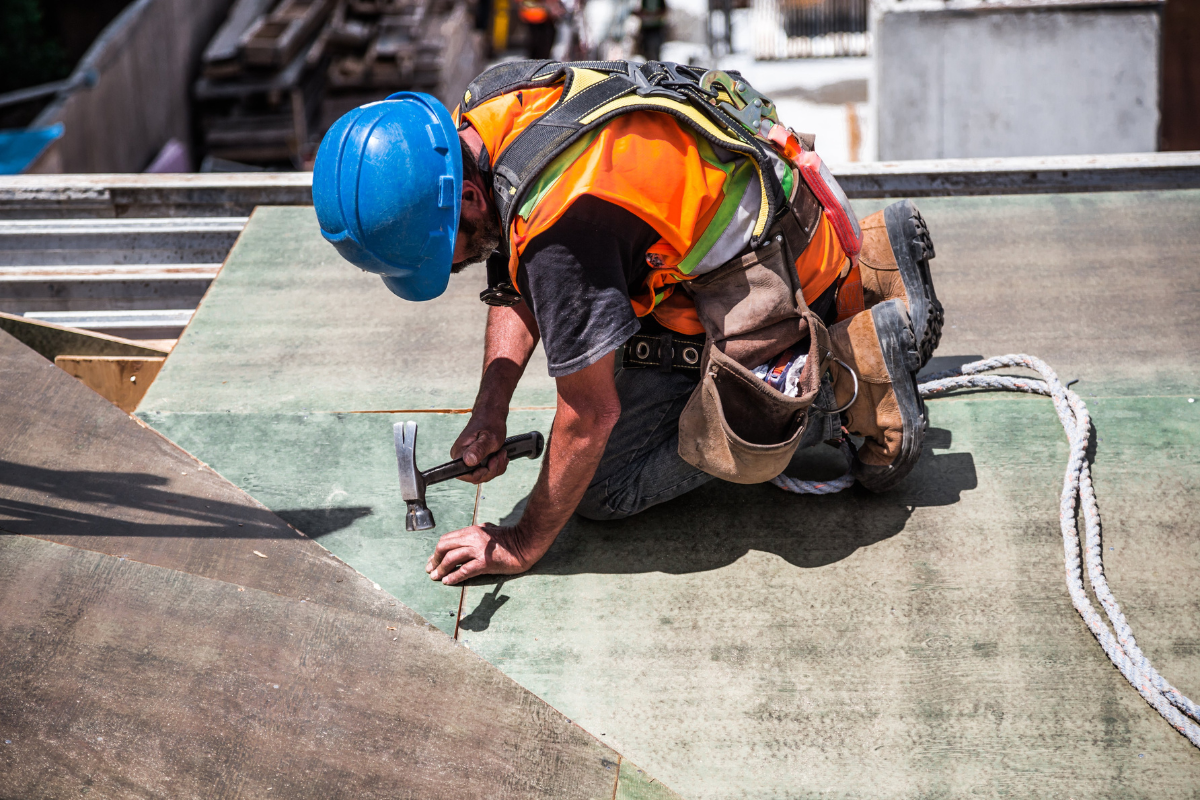
What Are the Benefits of Using Leading Indicators to Improve Your Workplace Safety Program?
According to the Occupational Safety and Health Administration (OSHA), using leading indicators to improve your workplace safety program can help:
- Prevent workplace injuries and illnesses
- Reduce the costs associated with workplace safety incidents
- Improve productivity and overall company performance
- Optimize safety and health performance
- Increase worker engagement and participation
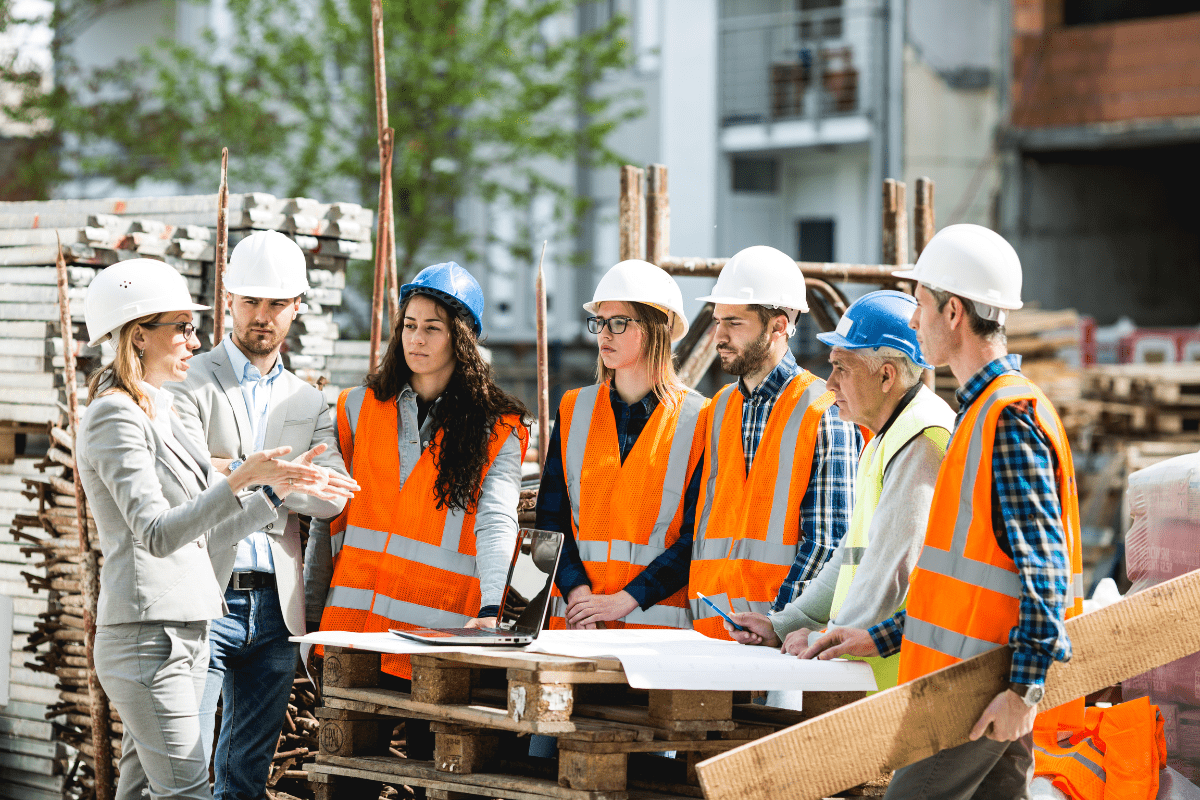
What Are Some of the Most Important Leading and Lagging Indicators in Workplace Safety?
The indicators that are most relevant to your company will vary depending on your industry, how your company is organized, and the types of risks your employees typically face.
Here are a few examples of leading indicators that may be relevant to your workplace safety program:
- Near Miss Reports – Near miss reports are incidents that could have resulted in physical injury and/or property damage but have not, either because of intervention or other factors. Tracking near misses can help you identify areas that present the highest degree of risk, allowing you to take corrective action before an accident occurs.
- Safety Training Participation – Compare incident rates for employees who complete safety training and those who do not. The numbers will likely show a higher risk of accidents among untrained individuals and can serve as a jumping-off point to mandate safety instruction for all employees.
- Safety Inspections – Tracking when incidents occur in relation to safety inspection dates may indicate a need for more regular inspections. If incidents still occur regardless of safety checks, the data may suggest that other issues are to blame, helping direct your attention to more pressing issues.
Lagging indicators that are relevant to many workplace safety programs include:
- Injury Rates – Charting the frequency of illness or injuries over hours worked will provide an exact incidence rate that can help your organization understand the overall safety performance of your company.
- Workers’ Compensation Claims – What are the most common types of compensation claims at your company? Are they associated with a particular workforce or specialization? Do they have an average cost? Tracking workers’ compensation claims can help you identify trends and patterns that may indicate a need for additional training or equipment upgrades.
- Lost Time Due to Injuries – Lost time is one of the most significant indirect costs of workplace injuries. Charting the production hours lost to missed work days will provide a clearer picture of the direct and indirect impact of accidents on your organization’s bottom line.
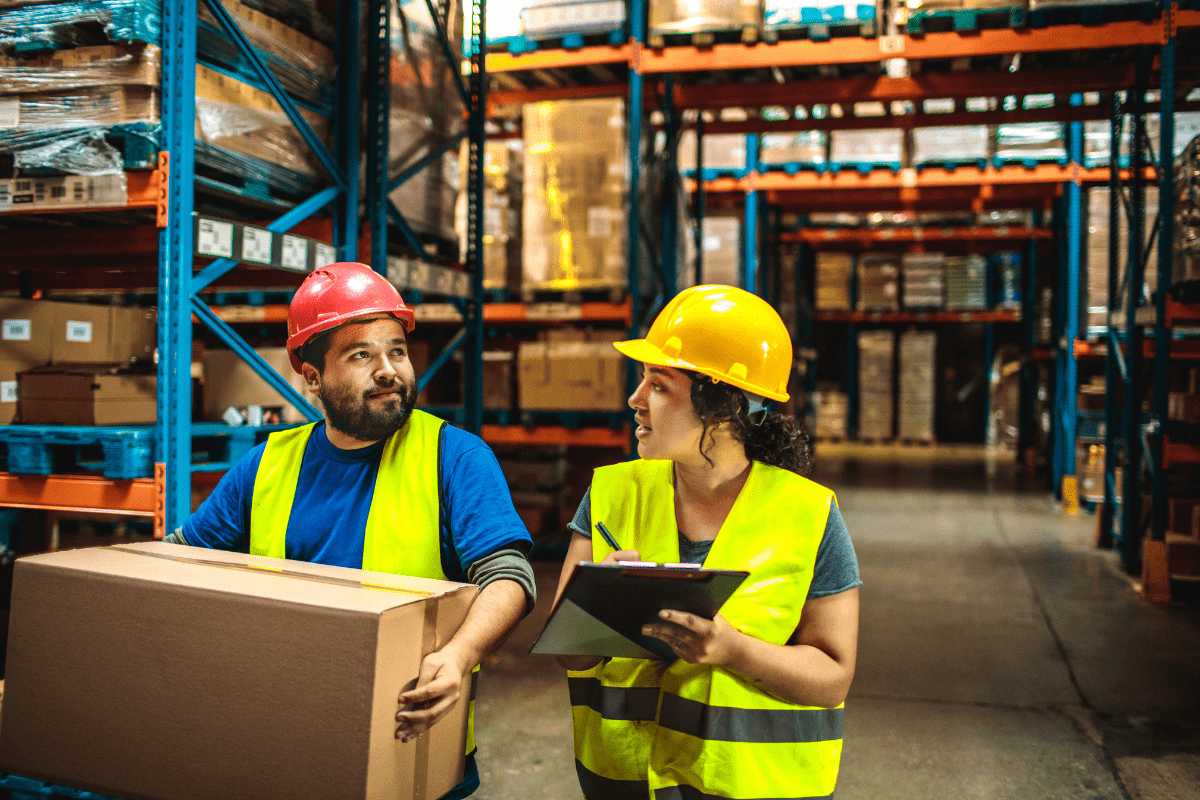
How Can Tracking Leading Indicators Improve Your Safety Record?
It’s easy to understand why taking preventative action is essential for reducing workplace injuries—however, to do so effectively, it’s necessary to understand where to focus targeted safety efforts within your company.
One recent study tracked injury factors in some of the most successful workplace safety programs. Researchers tried to focus on industries with the highest workplace safety risks, where preventative action would provide the most benefit, including construction, healthcare, and manufacturing.
The study found that “the use of leading indicators in conjunction with lagging indicators had a direct impact on the effectiveness of their workplace safety programs,” allowing employers to identify high-risk areas they previously overlooked.
The results were promising. More than 70% of study respondents stated that their leading indicator programs worked well and positively impacted the design and implementation of workplace safety practices, significantly lowering the volume of OSHA recordables among their workforce.
Looking to lower injury claims at your company and provide superior injury care to your team?
At OrthoLive, our mission is to get your injured employees back to work faster while providing the comprehensive support they need to stay healthy. Our platform offers 24/7/365 access to musculoskeletal support, wherever and whenever injuries occur.
Accessible through any device, OrthoLive’s system not only offers treatment with orthopedic experts in minutes, but provides a simplified process to track injury rates, helping you develop proactive safety strategies to lower the risk of OSHA claims among your workforce.
Find out how our platform can reduce your medical spending by 80% or more. Click here to see our product and service in action.