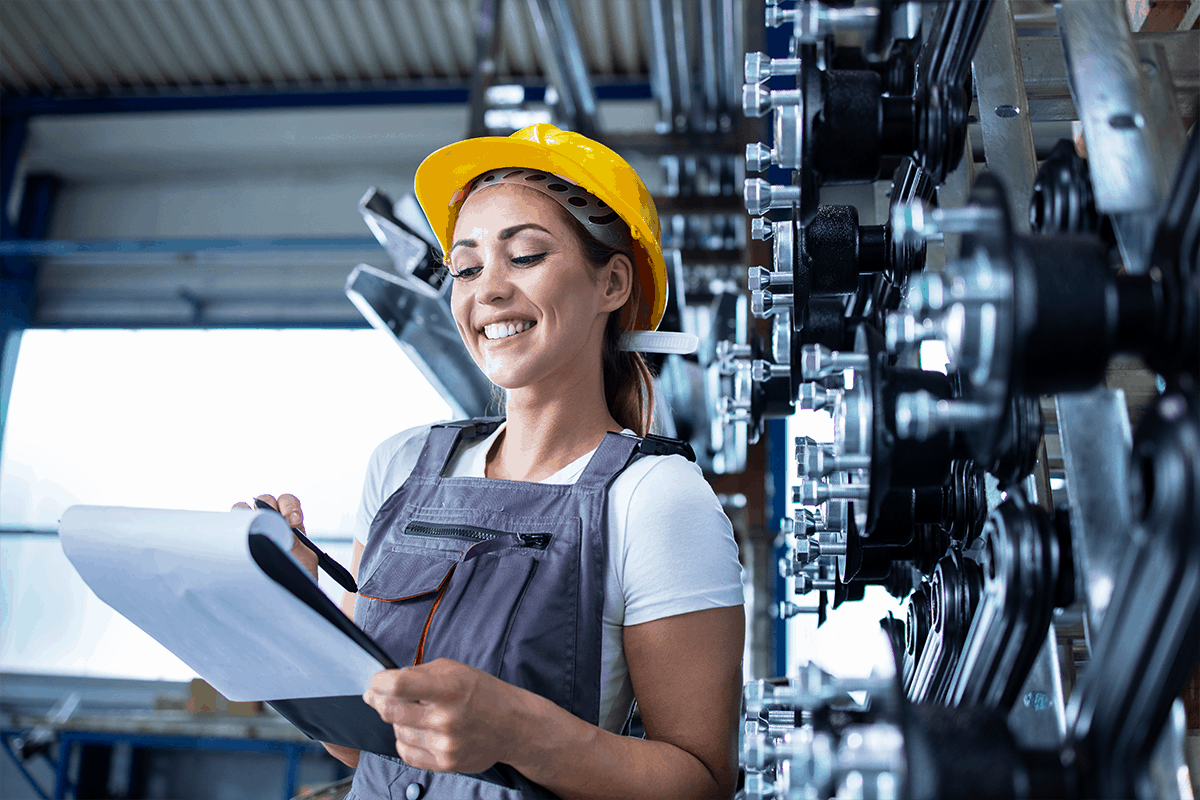
There is little doubt worker safety issues will be top of mind for employers in 2021. Risk & Insurance reports employers are spending $1 billion dollars each week on all of the connected costs of workplace injuries, including medical care, absenteeism, productivity losses, employee turnover, and workers’ compensation increases.
The United States Occupational Safety and Health Administration (OSHA) is the federal agency tasked with monitoring workplace safety. What can employers expect from this organization next year? What trends will affect workforce safety? Is there a cost reduction strategy aimed at employers that could reverse the costs of workplace injuries?
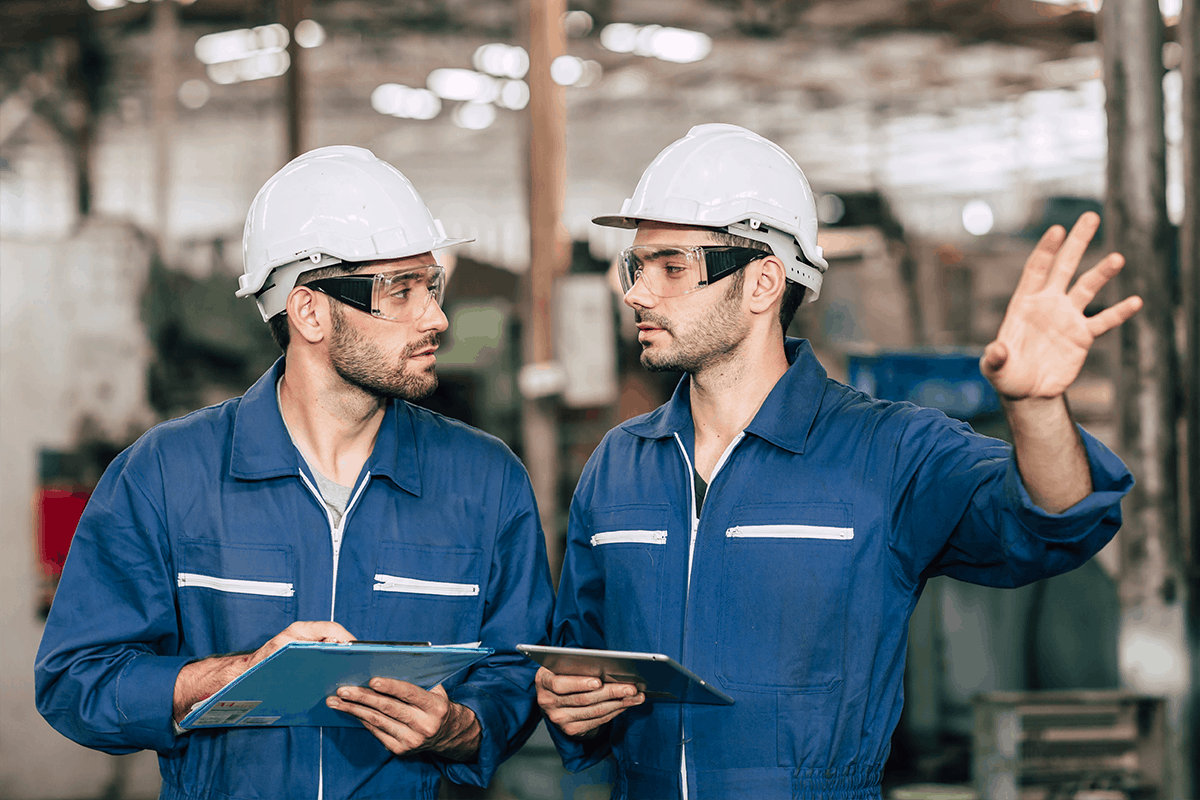
What to Expect from OSHA in 2021
The news from OSHA so far is that we can expect more inspections next year. The Congressional 2021 budget predicts the $12.7 million in additional funding will go toward hiring more Compliance Safety and Health Officers.
Predictions anticipate up to 500 additional workplace safety and OSHA compliance business inspections next year. Inspections of construction sites will make up more than 50% of these visits, according to Seyfarth’s workplace and environmental safety blog. Industrial Safety & Hygiene News (ISHN) reports some of the most common injuries on the construction job site include:
- Broken bones or fractures
- Burns or scarring
- Cuts and lacerations
- Head injuries
- Hearing loss
- Heat stroke
- Injuries to the spinal cord or back
- Limb or digit loss
- Repetitive motion stress injuries
- Vision loss
While construction is a large target for possible workplace injury and OSHA inspections, Seyfarth also says OSHA plans to continue their efforts to promote Site Specific Targeting (SST) inspections. Their efforts focus on non-construction workplace locations with 20 or more employees. SSTs are based on the OSHA Injury Tracking Application forms filed by employers when a workplace injury occurs.
Another prediction for 2021, according to the Seyfarth blog, is that a Presidential administration change could create “another dramatic agenda swing” is possible related to environmental regulation and worker safety. This administrative shift will likely change some of the proposed rule OSHA changes discussed in Construction Junkie this summer. At that time there were 24 OSHA proposed rule changes looming. They included primarily rule language clarifications, and changes to rules governing occupational exposure to natural and chemical exposure to chemical compounds.
The states are also expected to implement new regulations for COVID-19. In October, for example, the Division of Occupational Safety and Health of California (Cal/OSHA) issued new rules that define exposure to COVID-19 as an imminent hazard to workers, and the steps necessary for businesses to respond in the event this occurs. Cal/OSHA now requires notice of a potential exposure if the worker test positive for the virus.
While these are a few of the issues affecting OSHA activity next year, there are larger trends impacting worker safety that businesses should be aware of.

Trends Affecting Workplace Safety
Environmental Health and Safety (EHS) managers are closely monitoring a number of technology and workforce trends that will continue to impact companies next year.
Trend #1—Wearable Smart Devices
Internet of Things (IoT) personal protective equipment is changing how we monitor and improve workforce safety. IoT devices include a wearable sensor which is often embedded into the clothing of the worker. Biometric data is captured through WiFi on movement and worker activities that could impact their safety. These devices can proactively read and record heart rate and calories burned, steps walked and blood pressure.
These smart preventative tools are also growing more sophisticated and can read blood alcohol content, blood oxygen levels, sweat, and other vital signs. Health and safety teams can review that data online to determine if the employee is behaving in ways that could put them more at risks for a repetitive motion or other type of injury. With this data, the employee can be retrained on how to lessen their risk of injury. In the future, look for these devices to be more common with a higher level of tracking that could even measure worker fatigue and alertness.
Trend #2—Adaptable PPEs
Given that the COVID-19 pandemic is not over, we’re seeing a new line of personal protective equipment for industrial workers that reflect personal preferences. For example, there are now respirators that allow for workers with beards. Gloves are now lighter and more form fitting for added worker comfort.
New innovations in these areas are on the horizon; crowdfunding sites like Kickstarter are full of new designs for gloves, masks, and other PPEs, according to Smithsonian Magazine. There are face masks tailored to fit the contours of the individual’s face via 3D-printers and new mask braces designed to form fit the standard surgical mask to make it safer. There’s also the SEEUS95, a reusable N95 see-through biofilter that fits better than most masks while also allowing your workforce to share facial expressions hidden by the standard cloth mask.
Trend #3—Telemedicine for Injury Triage
The standard workflow for injury care in business is outdated and costly. When a workplace injury occurs, the typical response, no matter the severity of the injury is to call 911 in extreme cases but more generally to load the injured worker into a car and drive them to the ER. This means that even non-urgent injuries that just require self-care end up with a disproportionate response that costs the employer an OSHA reportable event, additional time off work, and hefty ER bills.
Businesses have begun shifting their injury response protocols to accommodate telemedicine. This technology connects the injured worker, manager, or health safety officer with a clinical professional through any handheld digital device. The healthcare provider can see the worker’s injury and make an immediate determination about the appropriate level of care. The cost savings in these cases is substantial.

Best Way to Reduce the Cost of Workplace Injury
Telemedicine has become a go-to for companies seeking to provide their workforce with on-site triage of their injuries. The OrthoLive Remote Injury Care program allows for immediate video conferencing with a clinical provider to assess and triage any injuries that occur on-site, 24/7/365.
Businesses adopting this approach save substantially on unnecessary ER trips while reducing OSHA recordable events. This is one workflow that literally pays for itself by reducing the costs of workplace injury. Talk with our team to find out how other employers are benefiting from this solution today.